Affiliate links on Android Authority may earn us a commission. Learn more.
Corning Gorilla Glass labs tour: Shattering glass for perfection
Published onFebruary 1, 2017
Today’s modern phones are made up of a ton of different components. Some of these components get more attention than others. Generally users tend to focus on the camera, or maybe the processor. Obviously the design itself is a big focus as well. One area that sometimes gets overlooked? That piece of glass laid on top of the touchscreen panel.
Looking closer at that sliver of glass, it’s something innocuous that we take for granted. When it comes to protecting all of today’s most popular mobile devices, there’s no other name that’s more highly recognized or acclaimed than Corning. Very recently, I was invited to the picturesque town of Corning, New York, which has some significance throughout history for the innovations and advancements we’ve seen with the art of glass making. In particular, this invitation centered around Corning’s reliability and testing labs, where they meticulously run routine tests on its glass, as well as competing ones, to ensure that their products live up to their claims.
To tell you the truth, this isn’t the first time I’ve been invited to check out what happens behind-the-scenes with a major company when it comes to quality assurance programs, so my initial thought was that they’d show me all the predictable “testing” they conduct – much to the same degree I’ve seen with previous tour visits. Coming out of this experience with Corning’s lab visit, however, I will certainly mention that my outlook and appreciation now has changed dramatically. There’s more to it than just the glass making!
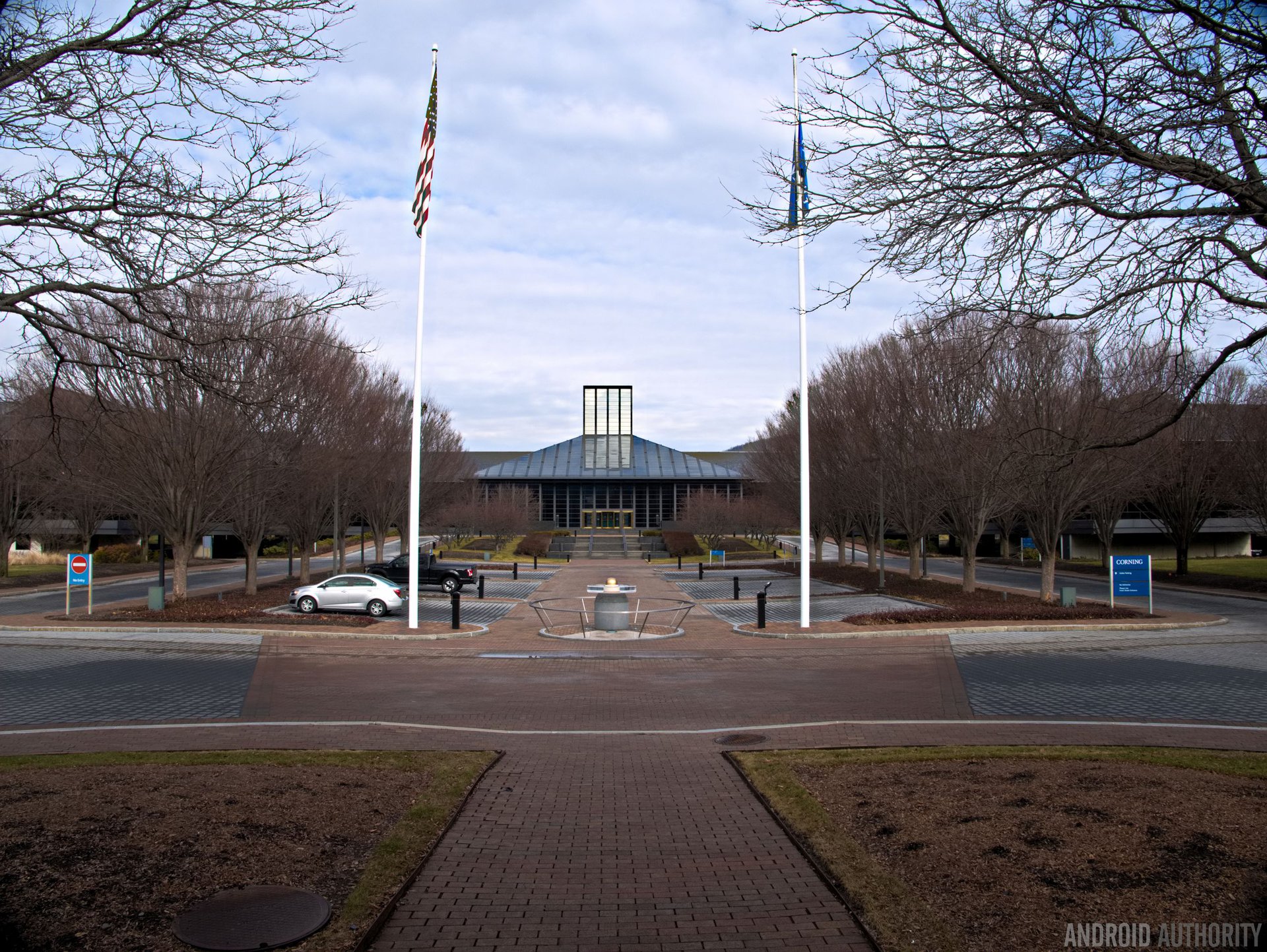
Controlled quality assurance testing
Okay, there’s a reason why Corning’s Gorilla Glass is found in many devices today – it’s the best at what it does! Now in its 5th generation (Gorilla Glass 5), its glass has a solid reputation that has helped to foster a consistent revolving door of “customers” (ie OEMs) coming back to them with their next products. With each iteration, the scientists over at Corning’s labs have set the bar higher by producing glass that’s stronger and more resilient to scratching – while also trimming its thickness. In all fairness, that’s a sentiment that anyone involved in tech shouldn’t be surprised to hear.
Taking us through a handful of testing areas in its labs, we were given several demos that I knew were all too predictable. From scratch testing competing glass against its product, such as non-treated/treated soda lime glass, you pretty much knew that Gorilla Glass would deliver outstanding resilience over the competition. Likewise, the same can be said about Gorilla Glass’ legendary tensile strength, as another demo had us rolling a heavy metal ball through a cylindrical chamber to land squarely on various glass. Not surprisingly, Gorilla Glass managed to hold up time-after-time – reinforcing the realization I already knew.
it’s amazing to see what goes into inspecting glass to meet certain standards
After these hands-on demonstrations, we were invited to check out some of the other restricted lab areas that handle more stringent controlled and real world testing. One particular machine applied tension on a piece of glass, while another one performed controlled drop tests at varying heights and slight angles – all of which are done in accordance to their strict quality assurance testing. Even though many of these machines are custom made, I’ve seen variations of the same machines at other testing facilities, so it wasn’t really all new to me.
Still, it’s amazing to see what goes into inspecting glass to meet certain standards. Most of the stuff we saw were controlled tests, but as we know, things happen quite differently in the real world, or what Corning scientist’s like to refer as “in the field.” Situations vary, but regardless, the folks in the labs have other machines that try to emulate what we put our smartphones through. For example, in testing Gorilla Glass’ scratch resistance, they place a mock device into a container filled with other things found in our pockets, like keys, pens, and other knickknacks, and tumble the container for a specified amount of time to see what happens to the glass.
Given Corning’s prestige and reputation, it makes perfect sense why they do the things they do – all in the name of quality assurance.
Microscopic imperfections, they compromise the strength of glass
Everything is bound to scratch and break, that’s just the reality. Even the hardest of substances, take for instance Sapphire, which is known far and wide for its scratch resistance, will eventually succumb to defeat in some way. Sure, Corning’s reliability labs showed us just how strong Gorilla Glass really is through its controlled tests, but it too is also capable of being broken/shattered.
And there’s a reason why that happens. In a perfect world, each piece of Gorilla Glass would be perfectly made through Corning’s fusion and ion-exchange processes. However, imperfections can happen at any time, but usually after the glass has been manufactured. Prior to my visit, I really didn’t really take the time to comprehend the nature of why glass shatters. I’ll be the first one to admit that I’ve shattered the Gorilla Glass on my smartphone after dropping it from a sizable height, but the scientists offered some additional insight.
Microscopic imperfections, those that are both visible and invisible to the eye, are the root causes to why even the strongest of glass can shatter or break. Throw in some other outside forces, such as applied pressure, tension, heat, and even chemical exposure, they all can impact the glass negatively. To be fair, though, there are other devices that I’ve used over an extensive amount of time, that have somehow survived several close calls.
Uncovering the root cause of glass failing
For us smartphone owners, we usually know why and how screens become shattered. Whether it’s by some exorbitant level of pressure, or clumsily dropping devices from our hands, the end determination is usually caused by the operator, which in this case is us; the owners. One of the biggest eye openers during my visit was how Corning’s scientists are capable of determining that exact reason, going as far to even sniff out the point of origin where the failure first manifests – leading to the cracks and webbed patterns forming the shattered glass.
Using high powered microscopes, it almost seems like Corning's fractography scientists are the NCSI division of the labs because they see what can't be seen.
One of the more intriguing parts of the labs tour was meeting up with the scientists that work in the fractography department, who inspect broken glass to determine the root cause of failures. Using high powered microscopes, it almost seems like they’re the NCSI division of the labs because they see what can’t be seen. Just like the patterns in our fingerprints, these fractography scientist can tell us the story behind a certain failure. Every single one of them is unique in their own way, and by inspecting various patterns and impact areas, they can uncover these imperfections and make a determination.
Pretty cool stuff if you ask me, seeing that there’s quite a lot involved in understanding the nature of glass!
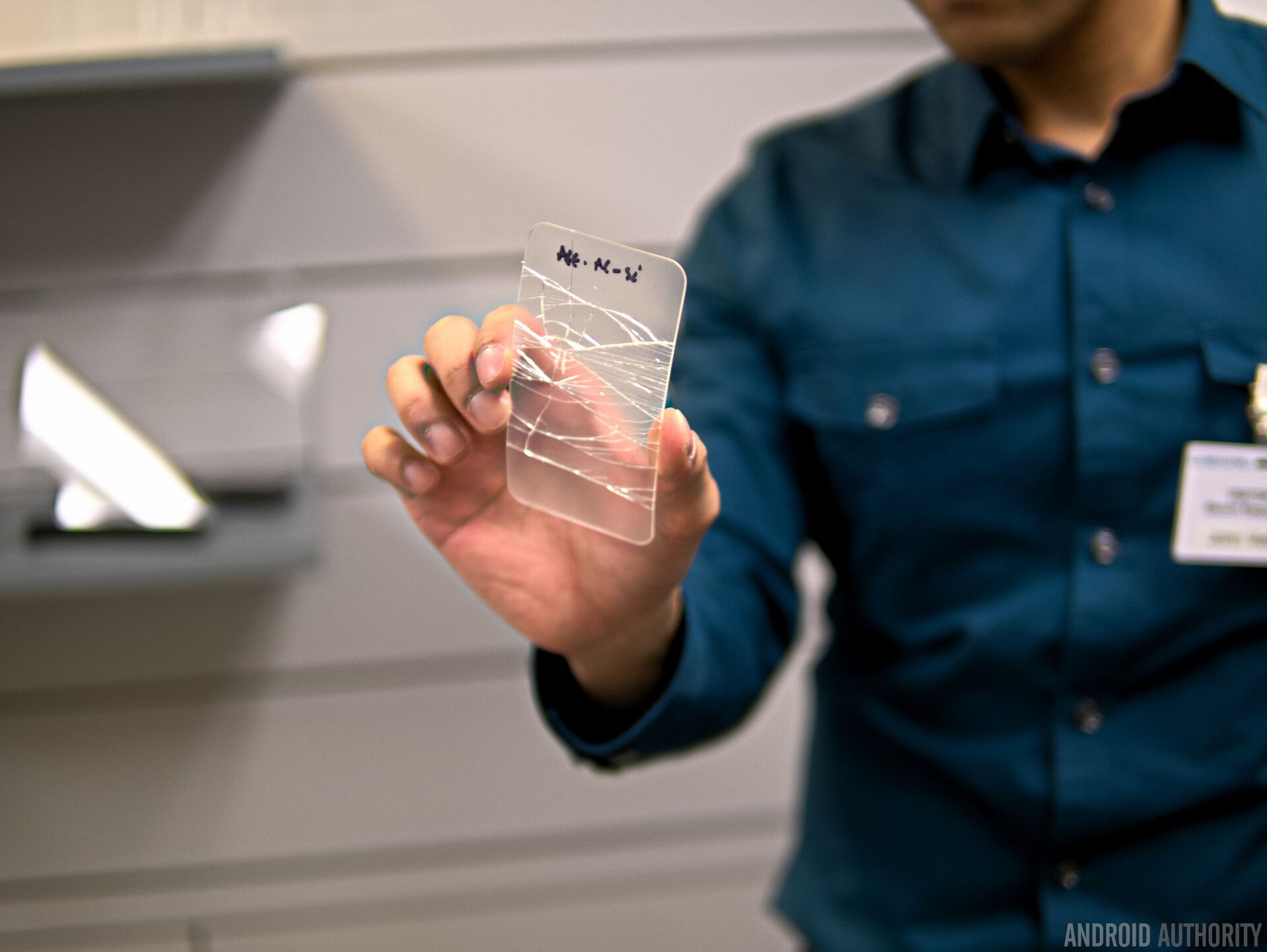
Environmentally respectful
So yeah, the Corning scientists shatter a whole lot of glass for the sake of testing – while also ensuring that their products meet their high standards. Obviously, all of these tests are necessary to back up Corning’s claim for Gorilla Glass, but what happens to all the glass shattered in the name of science? At the labs, they’re testing the next-generation of glass, so that comes with intellectual property that they don’t want to fall into the wrong hands.
In this particular case, the glass is disposed of appropriately. Later on after my visit, I was told that Corning recycles as much as they can back into their manufacturing process. There’s plenty of substance behind that because the company is strongly committed to protecting the environment, evident in the outline policy that’s stated on their website.
Overcoming the aesthetics
Again, we can’t stress about how Gorilla Glass on our smartphones and other mobile devices are underappreciated. Few folks ever really think about what goes into the entire process, which is probably why it’s an afterthought for many people until something catastrophic happens that forces us to think deeper about it. For starters, it’s more than just a rectangular piece of glass slapped over the touchscreen display.
Sometime during the halfway point of the labs tour, something peculiar dawned upon me. Knowing the kind of stringent testing Corning’s scientists put its products through, in addition to uncovering the reasons why even the strongest of glass can still shatter, I came to the realization that the aesthetics plays an important role with strength and integrity. Think about it for a second, as one solid, uniform piece of glass is manufactured to reach a certain standard. Once intentional imperfections are introduced, such as those cutouts for home buttons, earpieces, and even curved edges, the integrity and strength of the glass are modified.
With all of those cutouts and modifications, you can surely bet it has lost some of its resistive qualities. Therefore, they’re forced to work with its “customers” in order to properly design a piece of Gorilla Glass that meets its standards. This, of course, is a tough balance because you know that the development process for a phone is extended due to these modifications. The engineering is unbelievable when you think about how the strength and integrity of Gorilla Glass has increased with each iteration, while continually becoming skinnier!
Continuing to evolve
Needless to say, there’s a reason why Gorilla Glass is used by more phones than anything else. It’s no coincidence that billions of devices leverage it! The tour was definitely an insightful experience that made me realize that Corning has and continues to invest a lot of its resources to the research and development of Gorilla Glass. For them, it’s more than just shattering glass in its labs and facilities just for quality control, but rather, they’re striving for perfection! The next time you quickly peek at that notification on your phone, try to think about what went into making that sliver of glass. We sure will.